· Troubleshooting · 22 min read
Husqvarna Zero Turn Parking Brake Not Working
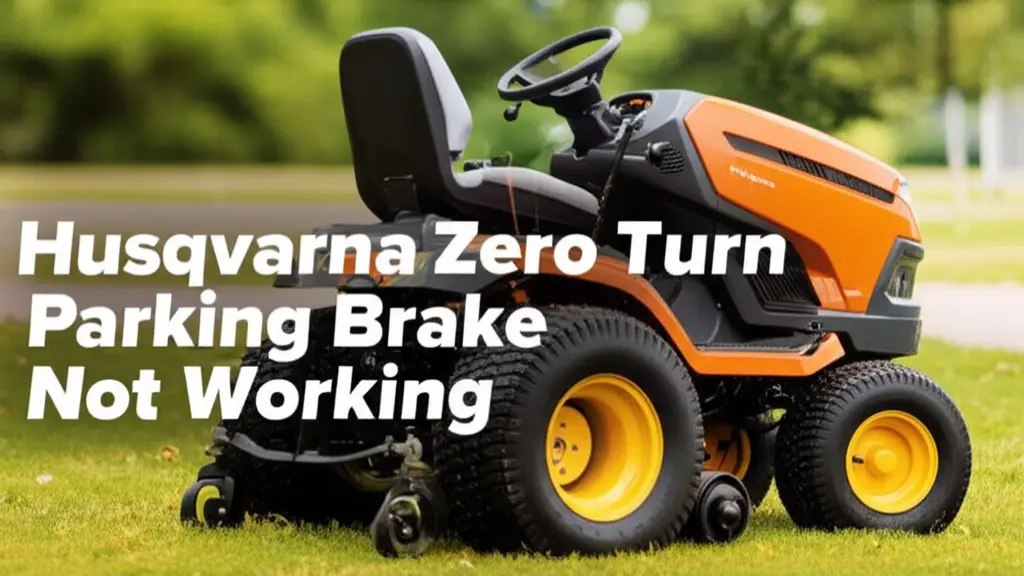
Husqvarna Zero Turn Parking Brake Not Working: A Complete Guide
Is your Husqvarna zero turn mower rolling away when you don’t want it to? A malfunctioning parking brake is a frustrating and potentially dangerous issue. This guide will walk you through the most common reasons why your Husqvarna zero turn parking brake isn’t working, and provide you with troubleshooting steps to get it fixed. We’ll cover everything from simple adjustments to more complex repairs, helping you regain control and safety while mowing. Let’s dive in and get your mower safely secured.
Takeaway:
- Check the parking brake cable for damage or looseness.
- Inspect the brake linkage for obstructions or wear.
- Verify the parking brake switch is functioning correctly.
- Consider hydraulic system issues if other problems exist.
Quick Answer: A Husqvarna zero turn parking brake not working is often due to a stretched or disconnected cable, a faulty switch, or issues within the hydraulic system. Inspecting the cable and switch are good first steps, but more complex issues may require professional help.
Husqvarna Zero Turn Parking Brake Not Working? Fix It Now!
Starting a Husqvarna zero turn mower for a productive day of yard work, only to find the Husqvarna zero turn parking brake not working, can be incredibly frustrating and a significant safety concern.
A properly functioning parking brake is crucial for both safe operation and to ensure the mower starts as intended.
This comprehensive guide will walk through understanding, troubleshooting, and repairing common parking brake issues, helping operators get back to mowing with confidence.
Quick Answer:
A Husqvarna zero turn parking brake that is not working typically indicates an issue with the steering lever engagement, worn mechanical components like cables or pads, or a malfunction in the mower’s integrated safety switch system. Diagnosing the exact cause requires systematic checks, from operator input to component inspection and electrical testing.
Problem: Husqvarna Zero Turn Parking Brake Not Working
Description: Understanding Your Parking Brake System
Understanding the fundamental operation of the Husqvarna zero turn parking brake system is the first step in diagnosing any issues.
This system is designed for both functionality and operator safety, integrating mechanical and electrical components seamlessly.
Integrated Steering Lever System
The parking brake on Husqvarna zero-turn mowers is ingeniously integrated with the steering control levers, making its operation intuitive yet critical for safety.
To engage the park brake, operators must move both steering control levers outwards from their neutral position. This outward movement physically activates the braking mechanism, securing the mower in place.
To release the park brake, operators need to pull both steering control levers inwards to the neutral position simultaneously.
This synchronized inward motion disengages the brake, allowing the mower to move. A critical aspect of this design is that if the levers are not brought inwards at the exact same time, the mower’s safety system will interpret this as an unsafe condition and shut down the unit.
This design choice underscores that the parking brake is not merely a mechanical component but a critical part of the mower’s electronic safety interlock system.
If the system detects an imbalance or incorrect sequence in lever positioning, it interprets this as an unsafe condition, leading to an immediate engine shutdown.
This means a “parking brake not working” symptom could actually be a safety system functioning as designed due to improper user input, or a fault within the safety switch network.
Therefore, troubleshooting should always begin with verifying correct operational procedure before assuming a mechanical fault.
Essential Parking Brake Components
The parking brake system relies on a network of mechanical components to translate lever movement into braking force.
These parts work in unison to ensure the brake engages and disengages smoothly.
Key components include the brake cables, which come in various lengths (short and long), and are responsible for transmitting force from the steering levers to the brake assemblies.
Brake arms and linkages then connect these cables to the actual braking mechanism at the wheels.
The actual stopping power comes from brake pads (or shoes, depending on the specific brake type), which are the friction material that presses against a brake drum or rotor to stop the wheel’s rotation.
Various springs, such as return and engagement springs, ensure that components reset correctly after the brake is applied or released.
Finally, an assortment of bushings, bolts, nuts, and washers secure the entire assembly and facilitate smooth pivot points throughout the system.
The detailed list of these components highlights the complexity of the mechanical system.
The fact that these components are subject to wear means that over time, even with proper operation, mechanical failure is a possibility.
The distinction between drum and disc brakes points to different wear patterns and maintenance considerations.
Drum brakes, while often more cost-effective and durable, are enclosed, making inspection and service more difficult, potentially leading to neglected issues. Understanding the individual components and their susceptibility to wear is crucial for accurate diagnosis.
A problem might not be with the main “brake” but with a small, seemingly insignificant part like a bushing or a spring, which can compromise the entire system’s function.
Component Name | Example Husqvarna Part Number (Note: Varies by Model) | Basic Function |
---|---|---|
ARM, BRAKE | 539132151 | Connects brake cable to the brake assembly at the wheel. |
GRIP, PARK BRAKE | 539105036 | The handle component used by the operator to engage/disengage the brake. |
CABLE, BRAKE, SHORT | 539132173 | Transmits mechanical force from the lever to the brake assembly. |
CABLE, BRAKE, LONG | 582122001 | Transmits mechanical force from the lever to the brake assembly. |
SPRING, RETURN | 575230201 | Ensures brake components return to their released position. |
SPRING, ENGAGEMENT | 575230301 | Aids in the positive engagement of the brake. |
BUSHING, BRAKE | 539132161 | Provides smooth pivot points for moving parts, reducing friction. |
ACTUATOR, SWITCH | 539132154 | Activates a safety switch based on brake lever position. |
LINKAGE, BRAKE | 596887001 | Connects various parts of the brake system to transmit motion. |
BRKT, BRAKE RT/LT | 575229602 / 575229702 | Mounting brackets for brake components. |
BOLT, SHOULDER | 539110303 | Fastener providing a pivot point for moving parts. |
NUT, HEX FLG NYLOC | 521996501 | Secures components, resisting loosening from vibration. |
Cause: Common Reasons Your Husqvarna Parking Brake Fails
A malfunctioning Husqvarna zero turn parking brake can stem from various sources, ranging from simple operational oversights to complex mechanical or electrical failures. Understanding these common causes is crucial for effective troubleshooting.
Operator Error and Misalignment
Sometimes, the issue isn’t a mechanical failure but a simple oversight or misunderstanding of the mower’s controls.
Failing to pull both steering control levers inwards to the neutral position at the same time when trying to release the brake can trigger the safety system, causing the unit to shut down.
This precise, simultaneous movement is a common point of confusion for operators. Similarly, if the steering controls are not locked in the neutral position when attempting to start the mower, the engine may not engage.
This suggests that operator habit or lack of precise control can be a leading cause of perceived brake failure, rather than a component malfunction.
User education on proper operation, especially the nuanced interaction with safety features, is as important as mechanical troubleshooting.
A simple adjustment in technique can often resolve the issue without needing parts or repairs.
Worn or Damaged Brake Cables
Brake cables are crucial for transmitting force from the control levers to the brake mechanism and are prone to various issues over time.
Cable stretch is a common problem, especially with regular use, leading to a loose or ineffective parking brake that reduces its holding power.
Over time, exposure to moisture, road salt, and other environmental factors can cause corrosion, weakening the cables and affecting their ability to transmit force and engage the brakes.
Cable binding occurs if cables are not properly lubricated or if debris accumulates within their housings, preventing them from moving freely and resulting in a stiff or non-responsive brake.
Furthermore, excessive wear, rubbing against other components, or accidental damage can cause fraying or complete damage to the cables, compromising their integrity and rendering the system ineffective.
The fact that environmental factors directly contribute to cable degradation points to the importance of protecting components from exposure, broadening the scope of “maintenance” beyond just lubrication and adjustment.
Worn Brake Pads or Shoes
Like any friction-based braking system, the brake pads or shoes on a zero-turn mower will wear down over time with repeated use.
When the friction material on these components wears thin, they lose their ability to create sufficient friction against the brake drum or rotor, leading to reduced holding power or complete failure.
If the brake pads do not engage tightly against the drum even after attempts at adjustment, it is a clear indication that they are worn and require replacement.
While adjustments can compensate for some wear, there is a point where the friction material itself is exhausted, requiring replacement.
Users might continuously adjust their brakes, masking the underlying issue of worn pads, which can lead to a false sense of security and eventually, complete brake failure.
Emphasizing inspection of pad thickness during adjustment is crucial for long-term safety and performance.
Issues with Linkages and Mechanical Parts
The complex system of linkages, arms, and pivot points that connect the steering levers to the brake mechanism can develop problems that significantly affect brake performance.
Loose connections or fasteners, such as nuts and bolts, can cause excessive play in the linkage, reducing the effective force transmitted to the brakes.
Bent components, including brake arms or linkages, can prevent proper movement or alignment, hindering brake engagement.
Accumulated debris, such as grass clippings or dirt, can obstruct the movement of linkages and pivot points, leading to binding or partial engagement of the brake.
Furthermore, a lack of lubrication on these pivot points leads to increased friction, stiffness, and accelerated wear, making the brake difficult to engage or release.
These issues, while seemingly minor individually, can cumulatively lead to the overall “parking brake not working” symptom.
The problem is often the culmination of neglected minor maintenance. Regular cleaning, inspection, and lubrication of these small, interconnected parts can prevent larger, more frustrating problems down the long run.
Safety Switch Malfunctions
Safety switches are designed to protect the operator by preventing unsafe operation, but when they fail, their symptoms can closely mimic parking brake issues.
A faulty seat switch, for instance, can cause the engine to shut off unexpectedly, even if the operator is seated, or prevent the mower from starting if it does not correctly detect operator presence.
Loose or frayed wires connected to these safety switches can lead to intermittent or complete failure, causing the engine to cut out or not start at all.
Debris stuck in a switch can also prevent its proper activation. The symptoms of a faulty safety switch (engine dying, no start) can be indistinguishable from a mechanical parking brake problem to an untrained eye.
This necessitates a clear diagnostic path that prioritizes checking these electrical components early, as they are often simpler to identify and fix than disassembling mechanical brake parts.
Manufacturer Recalls and Defects
While less common than wear and tear, some parking brake issues can stem from known manufacturing defects.
A notable recall occurred on July 8, 2009, for certain Craftsman Lawn Tractors, which were manufactured by Husqvarna.
This recall was initiated due to a parking brake cable failure that could lead to a loss of control. This type of recall highlights that specific components, like the parking brake cable, can sometimes have inherent weaknesses or design flaws that lead to widespread issues across a production batch. This means that some “parking brake not working” issues are not due to wear, tear, or operator error, but rather a fundamental flaw in a component from the manufacturer.
This shifts the responsibility and solution from the user to the manufacturer. Operators should always check for recalls related to their specific mower model, as this provides an alternative, potentially free, solution and underscores that not all problems are “fixable” by the user through maintenance or repair, sometimes requiring professional intervention under warranty or recall.
Solution: Troubleshooting and Repairing Your Parking Brake
Once the problem with the Husqvarna zero turn parking brake has been identified, the next step is to perform the necessary adjustments or repairs.
Many common issues can be resolved with a few basic tools and careful attention to detail.
Step-by-Step Troubleshooting Your Parking Brake
When facing a Husqvarna zero turn parking brake that is not working, a systematic troubleshooting approach can help identify the root cause efficiently.
Initial Checks and Easy Fixes
Before diving into complex repairs, it is always advisable to start with the simplest checks.
First and foremost, operators should consult their owner’s manual. This document is the primary resource for model-specific information, diagrams, and troubleshooting steps unique to the mower, often containing solutions for common issues.
Next, it is critical to verify steering lever position. Operators must ensure both steering control levers are moved fully outwards to engage the parking brake, or fully inwards simultaneously to release it.
Incorrect positioning is a very common cause of perceived brake failure or engine shut-off. Finally, operators should check for obvious obstructions.
A visual inspection for grass clippings, dirt, or other debris that might be physically blocking the movement of the steering levers or the parking brake mechanism itself can often reveal a simple fix.
By prioritizing these “human factors” and simple visual checks, operators can save significant time and effort, avoiding unnecessary disassembly or part purchases.
Testing Brake Engagement and Holding Power
Once initial checks are complete, it is important to test the brake’s effectiveness. A standstill test provides a clear indication of the brake’s holding power.
To perform this, park the mower on a level, dry surface and engage the parking brake fully. If applicable, disengage the transmission (often via bypass linkages).
Then, try to manually push the mower forward. The rear wheels should lock and skid, indicating proper brake engagement. If the wheels rotate, the brake needs service.
Another important assessment is the stopping distance test. If the mower requires more than five feet to stop when operating at its highest speed on a level, dry surface, the brake system needs immediate inspection and adjustment.
These tests provide a clear, quantifiable benchmark for when a parking brake is truly “not working” to a dangerous degree, prompting necessary action rather than delaying repairs based on vague symptoms.
This empowers operators to make informed safety decisions based on concrete evidence.
Diagnosing Safety Switch Problems
Safety switches are frequently the culprits when the engine will not start or cuts out unexpectedly.
A seat switch test can help diagnose this component. With the engine running, engage the PTO (blades).
Then, slightly raise off the seat. The engine should shut off. If it does not, the seat switch may be faulty.
For the parking brake switch test related to engine start, ensure the PTO is disengaged and the parking brake is not engaged.
Attempt to start the engine. It should not start under these conditions. If it does, the parking brake safety switch or its circuit is faulty.
For a more precise diagnosis, operators can use a multimeter to test the continuity of the seat or parking brake switch.
Typically, a good switch will show near zero ohms of resistance (continuity) in one state (e.g., plunger released) and infinite resistance (no continuity) when activated (e.g., plunger pressed in).
This process should be repeated for both sets of spades on a 4-prong switch. This level of detail helps operators understand why the test is performed this way, not just how.
It introduces the concept of circuit logic, which is crucial for troubleshooting electrical systems in general, moving beyond a simple “replace part” mentality to a more analytical approach.
Inspecting Cables, Pads, and Linkages
A thorough visual and manual inspection of the mechanical components is essential for diagnosing brake issues.
For cables, operators should look for signs of fraying, kinks, excessive slack (indicating stretch), or corrosion along the entire length of the brake cables. It is also important to ensure they move freely within their housings.
When inspecting brake pads or shoes, the rear wheels may need to be removed (as per adjustment steps).
Operators should then inspect the thickness of the brake pads or shoes. If they appear very thin or worn unevenly, they likely need replacement.
For linkages and pivots, all connecting rods, arms, and pivot points should be checked for looseness, bends, cracks, or excessive wear.
Operators should manually move these components to feel for binding, stiffness, or excessive play.
Finally, any accumulated debris such as grass, dirt, or other foreign material should be thoroughly cleaned from around the brake assembly, cables, and linkages.
While visual inspection is key, the manual “feel” test for resistance or looseness provides a more comprehensive diagnostic approach, especially for mechanical systems where subtle issues can have significant impacts that are not always visible.
Adjusting and Repairing Your Husqvarna Parking Brake
Once the problem with the Husqvarna zero turn parking brake has been identified, the next step is to perform the necessary adjustments or repairs.
Many common issues can be resolved with a few basic tools and careful attention to detail.
Adjusting Brake Tension for Optimal Performance
Proper brake tension is vital for effective and safe operation of the Husqvarna zero turn parking brake.
Step 1:
Prepare the Mower. Park the mower on a level surface, turn off the engine, and remove the key.
Engage the parking brake. For some adjustments, it may be necessary to jack up the rear of the mower and remove the rear tires to gain access to the brake assembly.
Step 2:
Locate Adjustment Points. Depending on the specific mower model, adjustment points may be found at the brake pads/drum assembly (often via an adjustment rod) or at the steering control pivot nut.
Always consult the owner’s manual for model-specific locations.
Step 3:
Adjust the Mechanism:
At the wheel (Drum Brake Type):
If adjusting at the wheel, operators will typically find a small pin secured by a clip. Pry off this clip gently with a flathead screwdriver or multitool, then pull out the pin to expose the adjustment rod.
Turn the threaded rod a few times to tighten the brake pad against the drum. Reinsert the pin and clip, then test the brake’s holding power.
At the steering control (e.g., Husqvarna Z254F):
For models like the Z254F, adjustment involves moving the boot covering the steering control base.
Then, tighten the 1/2-inch pivot nut until the braking action feels correct.
Step 4:
Repeat and Test.
It is crucial to adjust both sides evenly for consistent and balanced braking. After adjustment, perform the standstill test (as described in the troubleshooting section) to ensure the brake holds firmly and effectively.
The necessary tools for this process typically include a jack, a flathead screwdriver or multitool, and appropriate wrenches for lug nuts and pivot nuts, along with a brush or rag for cleaning.
The existence of distinct adjustment methods highlights that Husqvarna models can vary significantly.
The owner’s manual repeatedly warns that incorrect adjustment can lead to reduced braking ability and potentially cause an accident.
This underscores that while general steps are provided, consulting the specific owner’s manual for the user’s model is paramount to prevent applying the wrong procedure and to ensure safety.
Replacing Worn or Damaged Brake Cables
If inspection reveals stretched, corroded, or frayed brake cables, replacement is necessary to restore proper function.
Step 1:
Identify Correct Cable. Husqvarna offers specific part numbers for left and right, short and long brake cables.
Operators should consult their owner’s manual or an illustrated parts list to find the exact part number for their model. Genuine OEM parts are highly recommended for optimal fit and reliability.
Step 2:
Access and Disconnect Old Cable. This process often involves jacking up the mower, removing the rear wheel, and locating where the cable connects to both the brake assembly and the control lever.
Disconnect the cable ends and release it from any clips or guides that secure it along its path.
Step 3:
Install New Cable. Route the new cable exactly as the old one was, ensuring it is secured with all original clips and guides.
Connect the ends to the control lever and the brake arm/assembly.
Step 4:
Adjust and Test. After installation, it is critical to adjust the new brake cable tension as described in the “Adjusting Brake Tension” section.
Finally, test the parking brake thoroughly to confirm proper operation. The emphasis on using “original parts” for reliability and fit, along with the detailed process of routing the new cable, suggests that cable replacement is not trivial.
Incorrect routing of the new cable, even if the cable itself is correct, can lead to binding or ineffective braking, highlighting that replacement is not just about swapping parts but about precise installation.
Replacing Brake Pads or Shoes
When brake pads or shoes are worn beyond adjustment, they must be replaced to restore effective braking power.
Step 1:
Access Brake Assembly. Begin by jacking up the rear of the mower and removing the rear wheel.
This provides full access to the brake assembly located inside the wheel well. It is also a good practice to clean any debris from the area before proceeding.
Step 2:
Remove Old Pads/Shoes. This step typically involves disassembling parts of the brake mechanism, such as removing a pin and clip to free the brake pad from the drum.
Step 3:
Install New Pads/Shoes. Carefully place the new brake pads or shoes into position, ensuring they are correctly seated against the drum or rotor.
Step 4:
Reassemble and Adjust. Reassemble the brake mechanism, making sure to reinsert all pins and clips. Reinstall the wheel and lower the mower.
Crucially, operators must adjust the brake tension after replacing pads to ensure proper engagement and optimal performance.
The consistent mention of adjustment being necessary after replacing pads highlights that this is not a standalone repair but part of a larger process.
Users might replace pads but neglect this crucial adjustment step, leading to continued poor performance or premature wear of the new pads
.
Fixing Linkage and Pivot Point Issues
Addressing problems with the mechanical linkages and pivot points can significantly improve brake response and overall system reliability.
Remove all accumulated grass, dirt, and rust from the linkages, arms, and pivot points using a brush or rag.
This initial cleaning is vital as debris can cause binding. Tighten Loose Fasteners. Inspect all bolts, nuts, and clips securing the linkages.
Tighten any loose fasteners to eliminate excessive play in the system.
Lubricate Moving Parts. Apply a suitable lubricant to all metal-to-metal contact points, pivot points, and the parking brake cables.
For grease fittings (zerks) found on components like wheel axles, steering supports, deck lift pivots, and caster wheel pivots, use a pressure lubrication gun filled with #2 multi-purpose grease. Pump the gun until grease is seen flowing out of the bearing or bushing.
For exposed pivot points and cables, a spray lubricant like Lucas Oil’s “red n tacky” or a silicone-based lubricant is effective. A cable lubricator tool can be particularly helpful for applying lubricant directly into cables.
Caution:
It is important to avoid over-lubricating, especially near brake pads or drums, as excess lubricant can drip onto friction surfaces and reduce braking effectiveness.
Lubrication is not just a preventative measure; it can also restore functionality to stiff or binding linkages, effectively acting as a repair.
The distinction between different types of lubricants and application methods (grease gun for zerks versus spray for exposed parts) is a key detail for effective maintenance.
Addressing Safety Switch Failures
When safety switches are confirmed faulty, replacement is usually the most reliable solution to restore proper operation and safety.
Identify the Faulty Switch. Operators should use the diagnostic tests (engine start/stop scenarios, multimeter checks) to pinpoint the specific switch that is malfunctioning, whether it is the seat switch or a control lever switch.
Purchase a genuine OEM replacement switch for the specific mower model. Using genuine parts ensures compatibility and reliable function.
Replacement Procedure.
- Seat Switch: To replace a seat switch, unplug the wire harness, rotate the switch a quarter turn, and pull it out. The new switch can then be installed by reversing this process.
- General: Regardless of the specific switch, operators should ensure the wire harness is securely plugged in. It is also important to check for any damaged or frayed wires in the harness and repair them as necessary, as wiring issues can often mimic switch failures. Safety switches are critical for operator protection and integrated into complex electrical systems. Attempting to bypass or improperly repair these switches can lead to dangerous operating conditions, emphasizing the importance of proper replacement.
FAQs
Q1: Why does my Husqvarna zero turn mower shut off when I release the parking brake?
This is often due to the operator presence sensing system. If the steering control levers are not pulled inwards simultaneously to the neutral position, or if a safety switch (like the seat switch) is faulty, the system will shut down the engine for safety. This is a built-in protective feature.
Q2: How do I adjust the parking brake on my Husqvarna zero turn?
Adjustment typically involves accessing the brake assembly behind the rear wheels. It may be necessary to jack up the mower and remove the tire. Locate the adjustment rod (often secured by a pin and clip) and turn it to tighten the brake pad against the drum. Always refer to the specific model’s owner’s manual for precise instructions.
Q3: What are the main components of a Husqvarna zero turn parking brake system?
Key components include the steering control levers, brake cables (short and long), brake arms, linkages, brake pads (or shoes), brake drums/rotors, and various springs, bolts, and nuts. Safety switches, such as the operator presence switch and those on the control levers, are also integral to the system’s function.
Q4: Can a worn parking brake cable cause other issues on my mower?
Yes, a worn or stretched parking brake cable can lead to an ineffective brake, making it difficult to secure the mower. More critically, if the cable prevents the brake from fully engaging, it can prevent the engine from starting due to the safety interlock system, or cause the engine to shut off unexpectedly during operation.
Q5: How often should I check my Husqvarna zero turn parking brake?
It is recommended to check the brake operation frequently, ideally before each use or at least as part of a regular seasonal maintenance routine. This helps identify wear, damage, or misalignment early, preventing more significant issues and ensuring safe operation of the mower for every task.
Q6: Is there a recall for Husqvarna zero turn parking brake issues?
Historically, there was a recall on July 8, 2009, for certain Craftsman Lawn Tractors (manufactured by Husqvarna) due to parking brake cable failure. Operators should always check the CPSC website or contact Husqvarna/Sears for any active recalls specific to their mower’s model and serial number.
Q7: What kind of lubricant should I use for my parking brake linkages?
For grease fittings (zerks) on pivot points, use a #2 multi-purpose grease with a grease gun.
For exposed metal-to-metal contact points and cables, a spray lubricant like Lucas Oil’s “red n tacky” or a silicone-based lubricant is effective. Always clean the area before lubricating and avoid over-application.
Final Words
A functional Husqvarna zero turn parking brake is more than a convenience; it is a cornerstone of the mower’s safety and operational integrity.
By understanding how the brake system works, diligently troubleshooting common issues, and performing regular preventative maintenance—including timely adjustments, proper lubrication, and necessary part replacements—operators can ensure their mower remains reliable and safe.
Always prioritize safety, consult the owner’s manual for model-specific guidance, and do not hesitate to seek professional assistance for complex repairs.
Keep your Husqvarna running smoothly and safely for years of efficient lawn care.