· Lawn Mower Maintenance · 6 min read
Hydrostatic Transmission Slipping When Hot
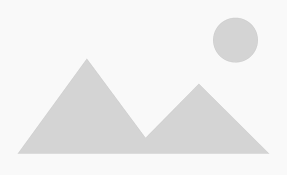
Hydrostatic Transmission Slipping When Hot: What’s Going On?
Have you noticed your lawn mower or other equipment with a hydrostatic transmission losing power or seeming to slip when it gets warm? This is a frustrating problem, but thankfully, it’s often fixable. A slipping hydrostatic transmission means the engine’s power isn’t efficiently reaching the wheels, leading to reduced performance. This article will dive into the common causes of this issue, how to diagnose it, and what steps you can take to get your equipment back in top working order. We’ll cover everything from low fluid levels to internal component wear, ensuring you have the knowledge to tackle this issue head-on.
Takeaway:
- Check your hydrostatic transmission fluid level and condition.
- Inspect for leaks around the transmission, pump, and hoses.
- Consider a fluid and filter change as preventative maintenance.
- If the problem persists, internal component repair or replacement may be necessary.
What causes a hydrostatic transmission to slip when hot?
A hydrostatic transmission relies on hydraulic fluid to transfer power. When the fluid heats up, it can become thinner, reducing its ability to maintain pressure. This loss of pressure is often the primary reason for slipping, especially under load.
Understanding Your Hydrostatic Transmission
Before we get into troubleshooting, let’s quickly review how a hydrostatic transmission works. It uses a variable displacement pump and a hydraulic motor to transfer power from the engine to the wheels. The pump pushes hydraulic fluid to the motor, which then drives the wheels. Adjusting the pump’s displacement controls the speed and direction of travel. Understanding this basic principle helps pinpoint where issues might arise when the system starts slipping. For more information on common problems, check out this guide to hydrostatic lawn mower transmission problems troubleshooting guide.
Low Hydrostatic Transmission Fluid: The Most Common Culprit
One of the most frequent causes of a slipping hydrostatic transmission is a low fluid level. As the fluid level drops, the pump can draw in air, creating bubbles in the system. These bubbles compress under pressure, reducing the transmission’s efficiency and causing it to slip. Regularly checking your fluid level is a simple preventative measure. You can usually find the dipstick near the transmission housing. Always refer to your owner’s manual for the correct fluid type and checking procedure.
Fluid Condition and Contamination
It’s not just how much fluid you have, but also what condition it’s in. Over time, hydrostatic transmission fluid can break down, becoming contaminated with metal particles and debris. This contamination reduces the fluid’s lubricating properties and can damage internal components. Dark, murky fluid is a clear sign it needs to be changed. Consider a complete fluid and filter change as part of your annual maintenance routine. If you’re experiencing issues with a Cub Cadet, you might find helpful information regarding oil changes here: cub-cadet-rzt-l-54-hydrostatic-transmission-oil-change.
Checking for Leaks in the System
Leaks are another common cause of low fluid levels and subsequent slipping. Carefully inspect the transmission housing, pump, hoses, and connections for any signs of leakage. Look for wet spots or drips. Even a small leak can gradually deplete the fluid level. Pay close attention to the areas where hoses connect to the transmission and pump, as these are common leak points. If you find a leak, address it promptly to prevent further fluid loss and potential damage.
Overheating and Pump Wear
When a hydrostatic transmission works hard, it generates heat. Excessive heat can cause the fluid to break down more quickly and can also damage the pump itself. Pump wear can lead to reduced efficiency and slipping, especially when the transmission is hot. This is often a sign of more significant internal wear. If you suspect pump wear, it’s best to consult a qualified mechanic. Sometimes, overheating is linked to other engine issues, like a Kawasaki engine that’s hard to start when hot: kawasaki-lawn-mower-engine-hard-to-start-when-hot.
Internal Component Wear: A More Serious Issue
If you’ve checked the fluid level, condition, and for leaks, and the slipping persists, the problem may lie within the transmission itself. Internal components like the pump swashplate, control valve, or motor can wear over time. This wear reduces the transmission’s ability to maintain pressure and transfer power efficiently. Diagnosing internal wear often requires specialized tools and expertise. In these cases, repair or replacement of the transmission may be necessary. If you’re dealing with a Cub Cadet XT1, you might find some helpful information here: cub-cadet-xt1-hydrostatic-transmission-problems.
FAQ: Hydrostatic Transmission Slipping When Hot
Q: How often should I change my hydrostatic transmission fluid? A: Generally, you should change your hydrostatic transmission fluid every 25-50 hours of operation, or at least once a year. Refer to your owner’s manual for specific recommendations. Regular fluid changes help maintain optimal performance and prevent premature wear.
Q: What type of fluid should I use in my hydrostatic transmission? A: Always use the fluid specified in your owner’s manual. Using the wrong type of fluid can damage the transmission. Hydrostatic transmissions typically require a specific type of hydraulic fluid designed for high-pressure applications.
Q: Can I add fluid to my transmission if it’s low? A: Yes, you can add fluid, but it’s crucial to identify why the fluid is low. Simply adding fluid without addressing a leak or underlying issue is a temporary fix.
Q: Is it normal for my transmission to get warm during operation? A: Some warmth is normal, but excessive heat is a sign of a problem. If the transmission is getting extremely hot, it could indicate low fluid, contamination, or internal wear.
Q: What does it mean to “disengage” a hydrostatic transmission? A: Disengaging the transmission allows the engine to run without powering the wheels, useful for transport or maintenance. You can learn more about disengaging a John Deere transmission here: how-to-disengage-hydrostatic-transmission-john-deere.
Conclusion: Keeping Your Hydrostatic Transmission Running Smoothly
A hydrostatic transmission slipping when hot is a common issue, but it’s often preventable with regular maintenance. Checking your fluid level and condition, inspecting for leaks, and performing timely fluid and filter changes are crucial steps. Remember, a properly maintained hydrostatic transmission will provide years of reliable service. If you’ve tried these troubleshooting steps and the problem persists, don’t hesitate to consult a qualified mechanic. Addressing the issue promptly can prevent further damage and save you costly repairs down the road. Don’t let a slipping transmission ruin your lawn care experience – take proactive steps to keep it running smoothly!